Июль 30th, 2013
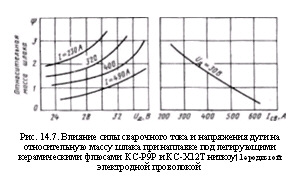
и др. и получения максимальной поверхностной твердости рекомендуется следующий режим термообработки: охлаждение после цементации с печью до 880—900 °С, закалка в масло.Распределение микротвердостн по толщине слоя на стали 20X13, охлажденной после цементации (950 °С, 8 ч, карбюризатор с 30% ацетата натрия) с контейнером иа воздухе, а также подвергнутой повторной закалке с 880 °С, хорошо иллюстрирует рис. 10. Мнкротвердость темной зоны на образцах, охлажденных вместе с контейнером, составляет Я100 = 250 МПа. В результате закалки она повышается до #100 = 4000-7-4500 МПа.Распределение углерода по толщине слоя исследовано во многих работах. На рис. 11 показано распределение углерода в цементованном 10 15 201 МП слое на стали 2X13 поданным [107]. Как видно на рисунке, поверхностная концентрация углерода определяется активностью карбюризатора и режимом насыщения.В работе [122] изучено распределение углерода и хрома по толщине слоя на стали 20X13 при образовании в процессе (950 °С, 8 ч) цементации на поверхности темной зоны (рис. 12, а, б). Содержание углерода по толщине темной зоны увеличивается, достигая максимального значения на границе темной зоны и зоны с высоким содержанием карбидов. Характер распределения хрома указывает на его диффузию в процессе цементации к поверхности.На рис. 13 показано распределение углерода по толщине слоя на стали 12X13 после нитроцементавди (950 °С, 3 ч) в газовой смеси 24% NH3 + 76% СН4.Рис. 13. Распределение углерода по толщине слоя на стали 12X13 после ни-троцементацни при 950 °С, 3 ч в смеси из 24% NH, + 76% СНЧРис. 13. Распределение углерода по толщине слоя на стали 12X13 после ни-троцементацни при 950 °С, 3 ч в смеси из 24% NH, + 76% СНЧ