Июль 30th, 2013
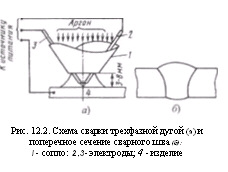
Во избежание выкрашивания слоя размер зерна должен составлять 7—12 баллов.Охлаждение некоторых аустенитных сталей, например высокомарганцевых, после азотирования не следует производить в атмосфере аммиака, так как это увеличивает хрупкость слоя. Хорошие результаты получены при охлаждении в среде полностью диссоциированного аммиака либо в продуктах сгорания керосина, аргоне и других восстановительных или нейтральных средах.Азотирование повышает износостойкость и уменьшает коэффициент трения ферритных и аустенитных сталей при нормальной и повышенных температурах. Коррозионная стойкость поверхностного слоя нержавеющих ферритных и аустенитных сталей в результате азотирования ухудшается.Ipn оптимальных условиях азотирования мартепсптпой п ферритной стали отпонностойкая зона занимает 50—80% глубины слоя. У стали переходного га эта зона составляет 35—45%. Аустеннтные стали имеют сравнительно [.шую зону низкой коррозионной стойкости —20—30% глубины слоя. {ля предотвращения коррозии в воде азотированных нержавеющих сталей ¦ Iточно их прокипятить в 10%-ном растворе бихромата калия в течение 1 ч следующей обработкой в 10—50%-ном растворе гидрофобизирующей кремне-ншческой жидкости ГКЖ-94 в бензине. Жаростойкость высокохромистых .рптных (мартенситных) и в меньшей степени аустенитных сталей после азо-гнрования понижается, кавитацнонная стойкость аустенитных сталей повы-шается [7]. , i ? Азотирование большинства аустенитных сталей позволяет получить слой толщиной не более 0,12—0,15 мм.С повышением температуры азотирования толщина слоя непрерывно возрастает, однако толщина высокоазотистой части слоя при температуре более 700— 800 °С заметно уменьшается.