Июль 30th, 2013
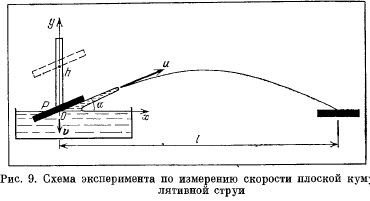
44.На быстрорежущих сталях толщина карбонитридного слоя не должна превышать 1—3 мкм, на штамповых 5—8 мкм. Общая толщина слоя составляетобычно 0,05—0,12 мм на быстрорежущих и 0,07—0,25 мм на штамповых сталях.Твердость азотированного слоя на этих сталях составляет HV 1100—1250.Азотирование повышает теплостойкость и задиростойкость штамповых сталей, а также препятствует налипанию жидкого металла на рабочую поверхность прессформы [11].Качество азотированного слоя определяют на образцах-свидетелях и непосредственно на деталях. Контролируют толщину слоя, твердость, коробление, размеры и качество поверхности (шелушение, трещины и пр.). Образцы-свидетели изготовляют из той же стали, что и азотируемые детали и подвергают термообработке.После азотирования летали подвергают визуальному осмотру. Азотированная поверхность деталей должна быть матово-серого цвета. Наличие цветов побежалости не является браковочным признаком. 100% деталей проверяют на отсутствие шелушения и трещин, особенно вдоль острых кромок при увеличении в 15— 30 раз. Контроль твердости проводят на образцах-свидетелях и непосредственно на деталях с помощью твердомеров типа «Виккерс» при нагрузке 50—100 Н и «Супер-Роквелл» при нагрузке 150 и 300 Н.Твердость несимметричных длинномерных изделий, склонных к короблению, следует контролировать также после окончательного шлифования азотированных поверхностей.Контроль хрупкости азотированного слоя производят в соответствии со шкалой хрупкости по виду отпечатка алмазной пирамиды.