Июль 30th, 2013
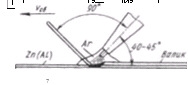
а) порошок алюминия или порошок ферроалюминиевого или ферроалюми-ниевомедного сплава (источник алюминия);б) порошок хлористого аммония или другого вещества (активатор процесса);в) порошок окиси алюминия или каолина (инертные добавки, предотвраща-ющие спекание частиц порошка алюминия или ферросплавов).Составы некоторых порошковых смесей для алитирования приведены в табл. 81.Перед использованием окись алюминия желательно прокаливать при 800— 900 °С. Активаторы вводят в смеси незадолго до применения. Все компоненты смеси тщательно перемешивают. Ферроалюминий обычно содержит 35—60% Fe; ферроалюминиевомедный сплав состоит из 37—47% Fe, 2—4% Си, остальное — алюминий с небольшими примесями марганца, кремния и др. [291, 292]. Все компоненты порошковых смесей просеивают через си го с размером ячейки 0,4— 0,5 мм.Алитирование в порошковых смесях ведут в специальных контейнерах РС плавкими затворами. Контейнеры изготовляют из 3—6-мм листовой жаростойкой стали, а также из углеродистых сталей, но в этом случае их нужно предварительно подвергнуть алитированию. По возможности контейнеры следует изготовлять соразмерно конфигурации самих изделий.Упаковку изделий, подвергаемых алитированию, производят так же, как и при других процессах ХТО. Полые и трубчатые детали следует упаковывать вертикально. Это уменьшает деформацию изделий и обеспечивает выход газов из полости детали.Контрольный образец кладут вместе с алитируемыми деталями.В процессе алитирования происходит некоторое ослабление активности смеси, что приводит к снижению толщины слоя. Многократное использование смеси — одно из условий успешного внедрения метода. Авторы работы [292] указывают, что при использовании смеси, состоящей из 99,5% сплава Fe—А1—Си и 0,5% NH4C1, для стабилизации активности смеси необходимо в отработанную добавлять 10% свежей. При низкой температуре (860 °С) смесь (99% FeAl+ + 1% NH4CI) можно применять многократно без освежения, добавляя после каждого режима 0,5—1,0% NH,C1 [296].