Июль 30th, 2013
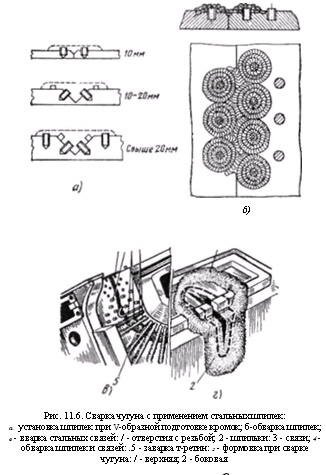
Влияние температуры и времени хромосилицирования в расплаве рекомендованного состава на толщину слоя показано в табл. 174.Тип покрытияГазовое хромосилицирование можно проводить в среде хлора при любых соотношениях феррохрома и ферросилиция в насыщающей смеси. При этом преобладает насыщение кремнием. Содержание кремния в слое (t = 980° С, т = 2 ч, FeCr : : FeSi =3:1) достигает 6—8%, а хрома — сотых долей процента. При замене газовой среды на Н2 -f- НС1 происходит одновременное насыщение стали хромом и кремнием [526].Используя различные методы и способы хромосилицироваиия и варьируя условия обработки, можно в широких пределах изменять строение, фазовый и химический состав хромосилицированных слоев, а следовательно, и их механические и физико-химические свойства.Поверхностная микротвердость хромосилицированных слоев, представляющих собой твердый раствор хрома и кремния в железе, составляет (в зависимости от условий насыщения и марки стали) 2500—4500 МПа. Она увеличивается с повышением содержания углерода в стали. Микротвердость карбидного слоя равна Я60 = 14 000-5-18 000 МПа.Микротвердость карбидной зоны на легированных сталях перлитного класса (20ХНР, 40ХН, 38Х2МЮА) составляет Я100 = 18 000-5-21 500 МПа, на сталях 20X13 и 25Х13Н2 Я100 = 14 000-5-18 000 МПа. Микротвердость о-фазы на стали 12Х18Н9Т не превышает Я100 = 5000-5-5500 МПа, а в зоне карбидов повышается до Я100 = = 12 500 МПа.Хромосилицированные средне- и высокоуглеродистые стали обладают высокой износостойкостью. По износостойкости в условиях сухого трения скольжения и абразивного изнашивания они не уступают борированным и хромированным сталям и значительно превосходят другие диффузионные покрытия. В результате хромосилицироваиия износостойкость стали 45 по сравнению с закаленным и низкоотпущенным состоянием повышается: в условиях сухого трения скольжения в 1,5—4,0 раза, в условиях абразивного изнашивания — в 1,5—2,5 раза (табл. 175). Хромосилицирование примерно в 3 раза повышает износостойкость инструментальных сталей ХВГ и Х12М [66, с.