Июль 30th, 2013
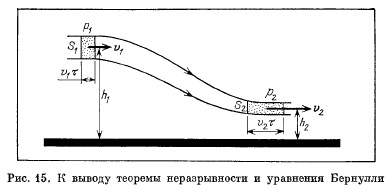
Помимо продолжительности холостого хода на снижение периода стойкости влияет и продолжительность рабочего хода, в течение которого происходит прогрев пластинки твердого сплава. При малом времени рабочего хода внутренние слои твердого сплава не успевают достаточно прогреться, а поэтому растягивающие напряжения при холостом ходе становятся значительно меньше, что приводит к меньшей потере стойкости. Подтверждением этого служат результаты эксперимента, изображенные на рис. 232. При фрезеровании детали шириной 130 мм фрезой диаметром 200 мм время холостого хода достаточно велико и составляет 0,3—0,4 с. Следовало ожидать существенного снижения стойкости фрезы по сравнению со стойкостью резца при непрерывном точении. Однако, как видно из рисунка, периоды стойкости практически совпадают, что связано с очень малым временем рабочего цикла (0,1 с).Возрастание времени холостого и рабочего ходов главного лезвия не может непрерывно сопровождаться уменьшением стойкости. Увеличение продолжительности холостого и рабочего ходов будет приводить к снижению периода стойкости только до тех пор, пока сохраняютсяусловия максимально возможного нагрева глубинных слоев и максимально возможного охлаждения поверхностных слоев пластинки твердого сплава. При дальнейшем увеличении времени холостого хода можно ожидать не снижения стойкости инструмента, а увеличения вследствие уменьшения числа циклов нагрева и охлаждения. По-видимому, стойкость инструментов при прерывистом резании определяется не только амплитудой изменения напряжений в поверхностном слое твердого сплава, но и числом этих изменений.Снижение стойкости инструмента при увеличении времени холостого хода происходит тем сильнее, чем меньшую прочность имеет инструментальный ма-60 eov.MtiuH -териал. Например, при точении стали 35Л резцом из наиболее прочного твердого сплава ТТ7К12 увеличение времени холостого хода от 0 до 0,06 с не влияет на период стойкости. Увеличение времени холостого хода до 5 с приводит к снижению скорости резания в 1,7 раза, а для резца из менее прочного сплава Т5КЮ — в 4 раза.