Август 2nd, 2013
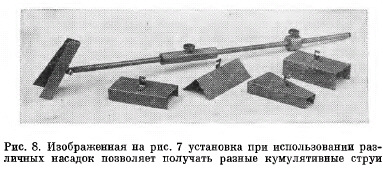
Достигается это по одной из следующих технологических схем.Отверстия диаметром до 50 мм (рис. 6.37, а) получают в два этапа: сначала центруют отверстие сверлом диаметром 12—15 мм на глубину 8—10 мм, а затем досверливают его на проход сверлом заданного диаметра. Предварительная центровка отверстия сверлом малого диаметра уменьшает вероятность отклонения от оси сверления и снижает усилие подачи сверла большого диаметра. В конце операции, если это предусмотрено конструкцией соединения, снимают потай (углубление на поверхности).Отверстия диаметром от 50 до 120 мм (рис. 6.37, б) выполняют по следующей схеме: центруют отверстие сверлом диаметром 12—15 мм на глубину 8—10 мм, сверлят на проход спиральным сверлом отверстие под направляющий хвостовик двузубого зенкера, а затем уже зенкером увеличивают отзерстие до требуемого диаметра.Отверстие свыше 120 мм (рис. 6.37, в) получают на радиально-сверлильных или горизонтально-расточных станках. В детали вырезают предварительно кислородным резаком отверстие с припуском 8—10 мм по радиусу. Полученное отверстие обрабатывают в размер с помощью оправки с резцом, которую закрепляют хвостовиком в шпиндель станка.Отверстие под развальцовку труб (рис. 6.37, г) должно обеспечивать повышенные требования по точности и шероховатости поверхности, его ПОДГОТаВЛИ Рис. 6.37. Типовые схемы получения отверстий:а —диаметром до 60 мм, б —от 60 до 120 мм, в —свыше 120 мм, г — под развальцовку трубеают по технологии, описанной выше, но дополнительно подвергают чистовой обработке с помощью разверток.