Август 11th, 2013
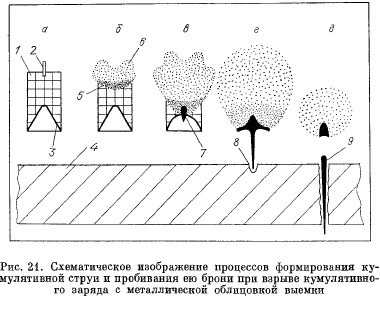
Порошковой металлургии железа посвящена уже обширная зарубежная и отечественная литература [66]. Поэтому мы ограничимся краткими замечаниями, относящимися к самому порошку.Качество железного порошка [см. 69] определяется прежде всего количеством содержащихся в нем окислов. Вследствие большой активной поверхности железного порошка, независимо от способа его получения, в нем всегда «имеются окислы. Кроме того, в порошке .могут содержаться окислы, связанные с условиями его получения. Наименьшее количество окислов содержит электролитический железный порошок, получаемый при дроблении в шаровых мельницах электролитического железа, осажденного при большой плотности тока. Наибольшее количество окислов содержится в порошке, полученном путем восстановления окалины, главным образом вследствие неполного восстановления последней. С уменьшением количества окислов в .порошке сильно возрастает предел прочности полученных из него железокерамических изделий и улучшается его прессуемость.Не менее важный фактор — сопротивление зерен порошка деформированию при сжатии. Это свойство порошка определяется в достаточной степени микротвердостью его зерен (рис. 13). Наиболее благоприятно сочетание свойств у отожженного электролитического железа. Зерна его компактные, осколочной формы (рис. 13, а) и имеют микротвердость 126 кгмм2, т. е. такую же как у феррита нормальной плотности. Изделие из такого порошка имеет плотное строение (рис. 13, б). Микротвердость зерен железа, восстановленного из окалины, вследствие их пористости, ниже (около 90 кгмм2); это ухудшает структуру и снижает качество изделия из такого порошка (рис. 13, в, г). Особенно вредны остаточные окислы, обнаруживающиеся в виде темно-серых включений с микротвердостью 330—340 кгмм2 внутри неполностью восстановившихся зерен порошка.